Понятие буфера времени является одним из основополагающих в Теории Ограничений Систем. Уровень запасов может быть выражен через категорию времени, как среднее время, необходимое для продажи всех запасов продукции на складе (например, у нас есть 6 недель запасов). Такое выражение запасов позволяет сотрудникам, отвечающим за выпуск и поставки продукции легче справляться с повседневными задачами. Информация о том, что на складе имеется 100 единиц продукции, может иметь значение для учета и финансового планирования с точки зрения стоимости этого объема продукции, но начальнику производства необходимо знать, достаточно ли запасов на складе, чтобы успеть получить пополнение или произвести дополнительный объем продукции. Ведь это влияет на повышение эффективности производства.
Однако, как известно, перевод количества запасов в единицы времени имеет свои подводные камни. Числовые значения, основанные на предыдущем опыте и средних показателях, являются прогнозами. Поскольку спрос постоянно меняется, частое использование временного эквивалента в измерении запасов теряет свою однозначность. Например, 400 единиц продукции и уровень продаж 100 единиц в неделю равняются 4 неделям продаж. Но что если в одну из недель продажи упадут до 80 единиц? В таком случае те же 400 единиц будут равны 5 неделям продаж. Что считать правильным? Увеличился ли объем запасов? Какие числовые показатели следует использовать? И как это делать?
Нам нужно уяснить, когда и как мы будем использовать количественные и временные показатели запасов продукции. В управлении запасами существует два типа решений:
- Планирование — определение адекватного уровня запасов.
На начальной стадии управления запасами, например, нового вида продукции, нам необходима точка отсчета – предварительная оценка (прогноз) того, какой объем продукции мы могли бы продать до того, как наши запасы будут пополнены. Эта оценка должна также учитывать возможные задержки, удлиняющие время пополнения запасов. Очевидно, что данное предположение будет строиться на категории времени а, следовательно, иметь определенную погрешность. Поэтому, нам необходим способ регулирования уровня запасов, основанный на актуальных показателях реализации (фактический уровень продаж).
Изменяясь с течением времени, фактический уровень продаж позволяет регулировать уровень запасов в сторону их увеличения или уменьшения. Алгоритм данной процедуры включает следующие вопросы:
— Имело ли место чрезмерное снижение уровня запасов? Имел ли место риск потери или потеря продаж?
— Оставался ли уровень запасов в течение длительного периода слишком высоким? Не слишком ли высок наш уровень запасов?
Эти решения основаны на оценке фактического уровня запасов.
- Производственные решения.
В ходе производства необходимо определять приоритеты, чтобы уложиться в производственный график. Эти решения также основаны на фактическом уровне запасов. Желательно, чтобы они повышали эффективность нашего производства.
Структура буфера запасов готовой продукции
Буфер запасов имеет следующую структуру:
- Базовый (целевой) уровень запасов (t) — представляет собой объем запасов, который подлежит пополнению. Поскольку мы всегда пополняем базовый уровень (Target level), объем продукции, отправляемый заказчику будет равен потреблению из буфера (Buffer Penetration) в момент, когда требуется пополнение запасов.
- Имеющееся количество запасов (oh) – этот тот объем продукции, который мы имеем на момент ее потребления (объем на складе).
- Критический уровень (красная зона) – это объем продукции на складе, обеспечивающий нам достаточное время для пополнения, в случае если потребление из буфера достигнет этого уровня.
Расчет степени проникновения в буфер (потребления из буфера):
Статус буфера (%) = (t − oh )*100 / t
Основная задача в рамках планирования – определить целевой уровень (t). Обеспечение данного уровня защищает от пиков спроса и задержек в цепочке поставок. Базовый уровень являет собой максимальный объем запасов в системе и равен общему объему складируемой продукции при условии незамедлительного пополнения запасов.
В момент, когда общий объем запасов опускается ниже целевого уровня, необходимо размещать заказ на пополнение запасов. Нетрудно заметить, что незамедлительное пополнение избавляет от необходимости прогнозировать величину базового уровня запасов. Вся процедура сводится к восполнению лишь того, что только что было продано или потреблено. Чем быстрее и надежнее ответная реакция производства на потребление продукции, тем меньше запасов нам требуется и тем ближе горизонт прогнозирования. Следовательно, повышается эффективность производства на склад и качество удовлетворения краткосрочного спроса.
Определение критического (красного) уровня
Критический уровень, иногда называемый «красной зоной», выполняет двоякую роль. С одной стороны, служит сигналом для пополнения запасов и средством защиты от потери продаж. Критический уровень посылает сигнал в момент времени, когда времени еще достаточно, чтобы пополнить запасы продукции. С другой стороны, данный показатель информирует нас об адекватности или неадекватности нашего целевого уровня и сообщает о том, нужно ли его увеличить. Объем запасов продукции необходимо увеличить, если он постоянно опускается до критического уровня. Многочисленные меры по ускорению производства для нас неприемлемы, поскольку они лишь привнесут хаос в производственный процесс. Чтобы избежать этих действий, наш базовый уровень должен быть достаточно высоким, что исключит частые и глубокие проникновения в критическую/красную зону.
В то же время целевой уровень должен быть достаточно низким, чтобы мы время от времени оказывались в ситуации, когда необходимо ускорить процесс и пополнить запасы. Отсутствие таких ситуаций – индикатор того, что у нас в наличии слишком большие запасы продукции.
Практика внедрения инструментов ТОС показывает, что в целях повышения эффективности производства наиболее приемлемо установить красную зону на уровне одной трети целевого объема запасов. Данная величина критической зоны, задаваемая по умолчанию, позволяет ей выполнять обе функции – своевременно сигнализировать о необходимости пополнения и информировать о степени адекватности целевого уровня. При этом, как показывает практика, нет необходимости в дальнейшей оптимизации соотношения 1/3, поскольку эти действия не принесут значительной добавочной стоимости.
Законы Эли Голдратта по управлению запасами в сфере дистрибуции
Поскольку Теория Ограничений Систем уже предложила свои решения для систем дистрибуции, почему бы не переложить эти принципы на процесс управления запасами?
1. Когда происходит проникновение в «красную» зону, отслеживайте глубину этого проникновения. Если оно слишком глубокое или длится долгое время, следует увеличить целевой уровень запасов. Значения «слишком глубокое» и «долгое время» зависят от требуемого качества услуг в вашем бизнесе, а также от степени риска истощения запасов, на который вы готовы пойти. Безусловно, если потребление захватывает всю красную зону (или ее большую часть), целевой уровень запасов должен быть увеличен. Доктор Голдратт рекомендует устанавливать целевой и критический уровни запасов, опираясь на степень потребления из красной зоны. Если уровень потребления в течение среднего времени пополнения был равен или превышал критический уровень, следует увеличить целевой уровень на 33%, тем самым увеличив и объем критической зоны.
2. В случае если в течение всего периода пополнения имеющийся уровень запасов оставался в «зеленой» (безопасной) зоне, следует сократить целевой объем запасов на 33%. Рекомендуемая величина увеличения и уменьшения (33%) позволяет наиболее оперативно реагировать на изменения спроса.
3. Каждый раз, увеличивая целевой объем запасов, прежде чем диагностировать уровень запасов, следует дождаться окончания следующего цикла пополнения. Вносить изменения по увеличению или уменьшению объема продукции следует только после завершения второго цикла пополнения запасов.
4. Каждый раз при увеличении целевого уровня, первое время общий уровень имеющихся запасов оказывается выше, чем ваш новый целевой уровень (при условии, что вы снизили буфер на 33% и «зеленая», безопасная зона также составляет 33%). Прежде чем диагностировать, следует дождаться момента, когда объем запасов станет ниже безопасного уровня. Только после этого можно проводить проверку и дальнейшее снижение целевого уровня.
Необходимо отметить, что вышеперечисленные рекомендации носят общий характер и, поэтому, в конкретном производстве должны применяться с особой осторожностью. 33%-ое увеличение целевого уровня может привести к выпуску относительно крупных партий одного вида продукции и задержкам производства иных видов продукции. Это чревато целым шквалом увеличений целевого уровня и выпуском крупных партий. В результате возрастания нагрузки на ограничение (ресурс, мощность которого меньше той мощности, который от него требует система) повышается потребление из «красной зоны», что приводит к задержкам производства продукции. Чтобы избежать этого, рекомендуется использовать следующий принцип: если вы повышаете целевой уровень какого-либо изделия, следует разбить это повышение на две или более партии, чтобы не вызвать задержки в производстве других заказанных изделий.
Источник: Drum Buffer Rope and Buffer Management in a Make-to-Stock Environment (март, 2007 / www.ScienceofBusiness.com)
Авторы: Scharagenheim и Burkhard
Переводчик: Е.С. Белов
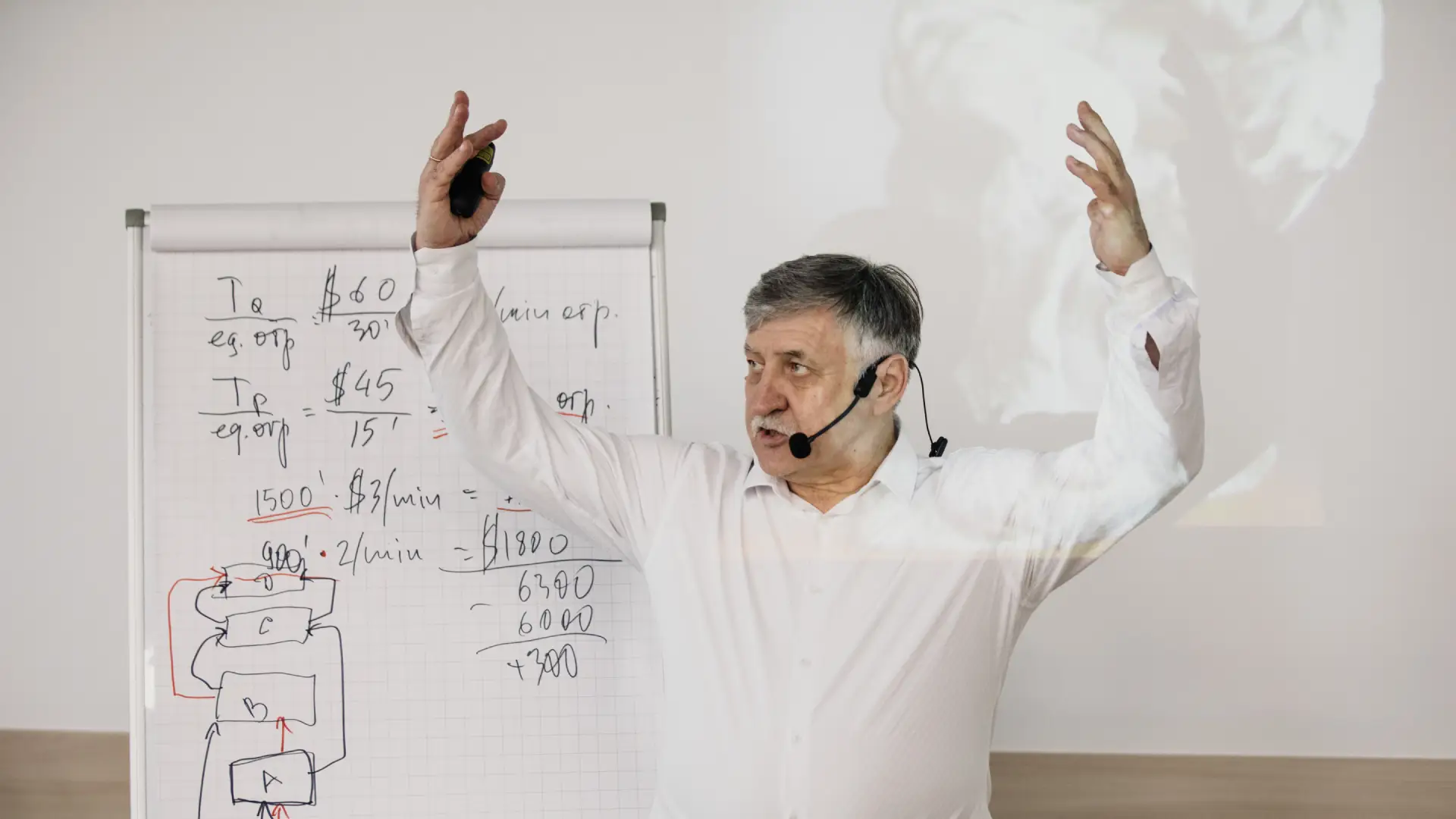
Управление производством по ТОС
На онлайн-курсе вы познакомитесь с подходом Теории ограничений и сможете управлять своим предприятием более эффективно. Инструменты ТОС, такие как Барабан-буфер-канат, сокращают производственный цикл и незавершенное наполовину, а уровень выполнения заказов в срок достигает более 95%.
Тренеры: В.В. Вальчук, В.Е. Краснов. Старт: 3 июня 2024.
ПОДРОБНЕЕКнига в подарок
Опубликована наша книга «Прорыв. Единственный путь развития бизнеса». Это бизнес-роман о производственном предприятии, столкнувшимся с «потолком» в своем развитии. Для прорыва в развитии руководству и персоналу приходится преодолеть собственные, выстраданные на опыте, но устаревшие убеждения. Читателю предлагается пройти через этот прорыв вместе с героями. Вы увидите трудности такой трансформации, осознаете природу сопротивления изменениям и реальный путь к таким изменениям.
Подпишитесь на наш Telegram-канал и получите книгу в подарок!
Похожие статьи
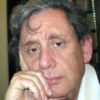
Eli Schragenheim,
CEO of Elyakim Management Systems (1992) Ltd